2024 Training Courses
- May 9, 2024 -
The 2024 Training Courses have been set!
​
The 2024 Calgary Pump Symposium will host 5 full day paid training courses on May 9th, 2024, the topics of which are outlined below. Once the instructors have been finalized this page will be updated with their information.
​
The 2024 course offerings are:
Course 2 - Centrifugal Pump Fundamentals
Course 3 - Electric Motors and Variable Frequency Drives
Course 5 - Pump piping system design to avoid vibration and fatigue failures
Course 1​ - Slurry Pumps
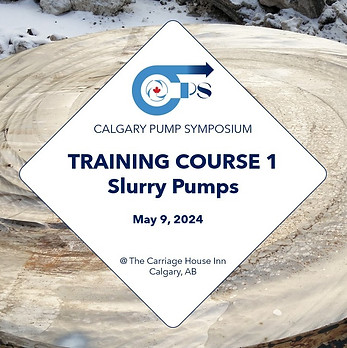
Description:
This expanded course will cover the specification, operation and maintenance of slurry pumps used in a wide variety of applications. The focus will be on the differences between slurry and non-slurry pumping applications, with many real-world examples given. This course is intended for engineers and technicians who are involved in the specification, reliability improvement or operation of slurry pumping systems.
Course 2​ - Centrifugal Pump Fundamentals
Course 3​ - Electric Motors and Variable Frequency Drives
Course 4​ - Mechanical Seals
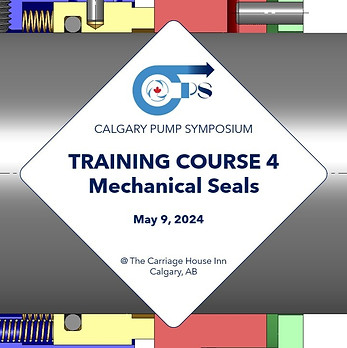
Description:
This course is aimed at professionals that are end users, OEM, Project or contractor personnel who work with or specify rotating equipment in the chemical or hydrocarbon processing industry. The course will focus on basic and advanced concepts with the aim of providing attendees with a working knowledge of mechanical seals and sealing systems.
Course 5​ - Pump piping system design to avoid vibration and fatigue failures
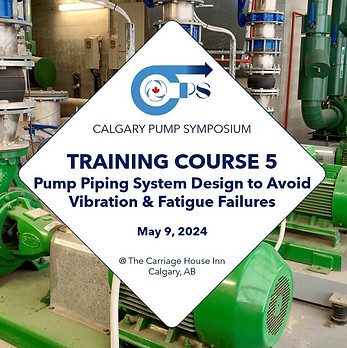
Description:
The goal of this short course is to provide insight into the design considerations and industry best practices for reciprocating and centrifugal pump installations to minimize vibration that can lead to fatigue failures of mainline and small bore piping.
​
Background:
Industry surveys show that more than 20% of unplanned product releases are due to fatigue failures caused by vibration. These product releases have an immediate impact on the reliability and economics of operating machinery assets as well as posing significant safety and environmental risks. Piping designers are often unaware of the specific requirements for fatigue and vibration control in a vibratory service such as piping in a centrifugal and reciprocating pump installation. Solving fatigue and vibration problems after a project has been completed or commissioned is costly and results in significant downtime.
​
Who Should Attend:
This short course is for engineers, managers and technical staff involved in the design, commissioning and installation of industrial centrifugal and positive displacement pump and piping systems.